3D 打印模型支撑优化:软件算法与手动调整的完美结合
随着3D打印技术的快速发展,越来越多的行业开始利用它进行产品原型设计、零件制造以及其他应用。然而,3D打印过程中往往会遇到一个难题——支撑结构的设计与优化。支撑不仅影响打印质量,还关系到后处理的难度和打印成本。为此,如何通过优化支撑结构提高打印效果,减少材料浪费,成为了业内关注的重点。本文将详细介绍3D打印模型支撑的优化方法,重点阐述软件算法和手动调整如何协同工作,实现最佳支撑结构。
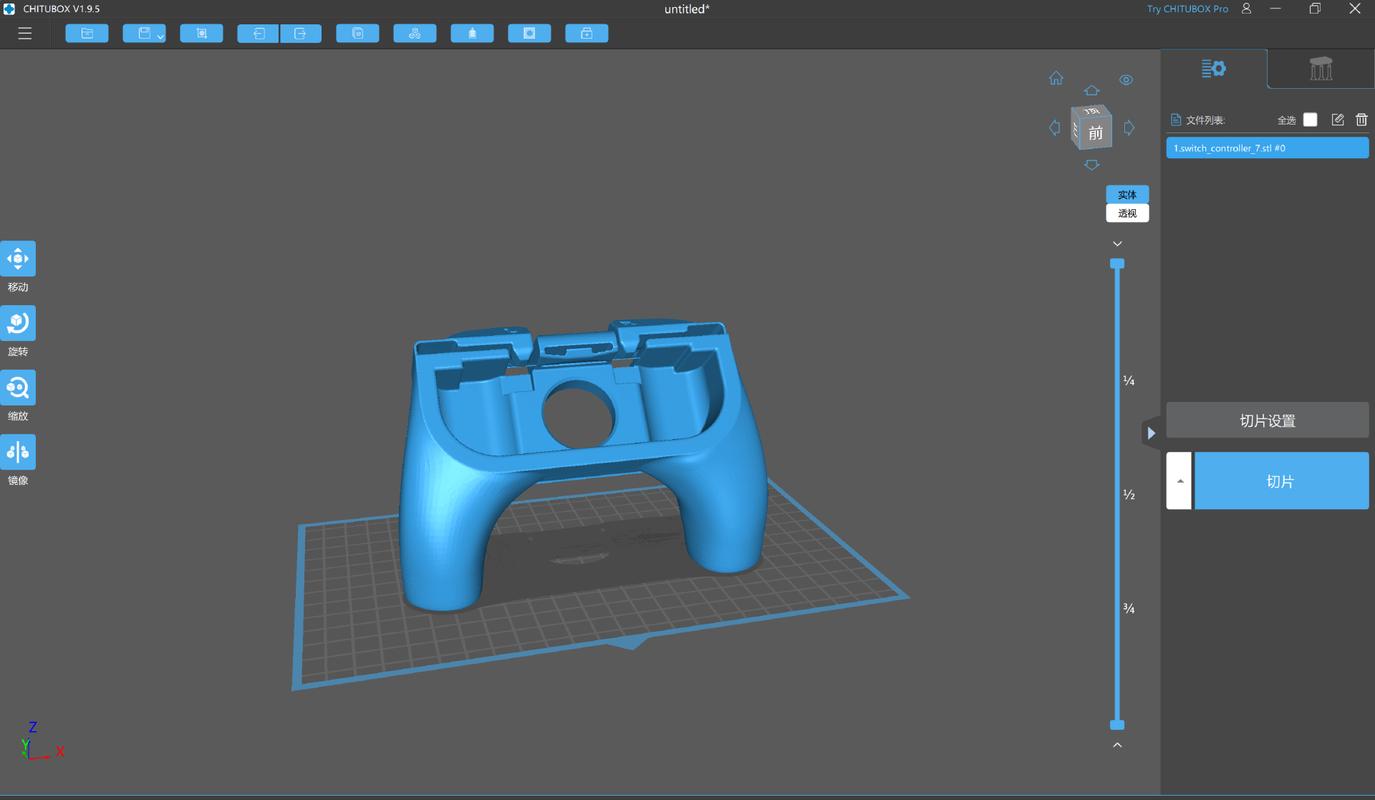
一、3D打印模型支撑结构的作用
在3D打印过程中,支撑结构是用来支撑悬空部分的关键组件。由于大部分3D打印技术采用逐层堆叠的方式,如果没有支撑结构,打印机将无法正确打印出悬空或超出支撑的部分。这些支撑结构在打印完成后,通常需要手动拆除,甚至需要后处理才能获得光滑的表面效果。因此,如何设计一个既能提供足够支撑,又便于拆除的支撑结构成为3D打印设计中的一项重要任务。
二、支撑优化的挑战
支撑结构的设计不仅仅是为了避免模型掉落,还涉及多个方面的优化问题:
1. 支撑的强度与稳定性:支撑结构必须足够强大,能够承受打印过程中模型的重量,防止发生倾斜或脱落现象。
2. 后处理难度:支撑结构一旦设计不合理,拆除时可能会对模型表面造成损伤或留下痕迹,增加了后期的工作量。
3. 材料浪费:不合理的支撑设计会导致不必要的材料浪费,尤其是在大尺寸或复杂模型时,支撑结构的材料消耗可能非常庞大。
4. 打印时间:过多或不合理的支撑结构可能会增加打印时间,影响整体生产效率。
因此,支撑结构的优化不仅仅是简单的设计问题,还涉及成本、时间和后处理等多个方面的综合考量。
三、软件算法在支撑优化中的应用
随着计算机辅助设计(CAD)技术和3D打印软件的进步,支撑结构的设计已经不再完全依赖手动调整。许多3D打印软件采用了先进的算法来优化支撑结构,具体方法包括以下几种:
1. 自动生成支撑结构
许多3D打印软件,如Cura、PrusaSlicer和Simplify3D,已经具备自动生成支撑结构的功能。软件可以根据打印模型的几何形状,自动计算需要支撑的部分,并生成相应的支撑结构。这些软件通过算法分析打印模型的形状,判断哪些部分需要支撑,哪些部分可以通过改变打印角度避免支撑,从而优化支撑的生成。
2. 优化支撑密度与接触点
除了自动生成支撑外,软件还能够根据打印需求优化支撑的密度和接触点。例如,对于较小的悬空部分,可以减少支撑的密度,以减少材料的使用和后处理的难度。而对于较大的悬空部分,软件则可以增加支撑密度,确保稳定性。通过这些算法,软件能够在支撑强度、材料浪费和后处理难度之间找到平衡。
3. 自适应支撑与可调参数
许多现代3D打印软件支持自适应支撑的生成,即根据打印模型的不同区域自动调整支撑结构的类型和密度。用户可以根据模型的具体需求设置参数,如支撑角度、支撑类型(如树枝型、网格型或线条型)等,软件会自动生成适合的支撑结构。这样,用户可以在打印过程中最大程度地减少材料浪费,并减少后处理的麻烦。
四、手动调整:精细化的支撑优化
虽然现代3D打印软件提供了强大的自动支撑生成算法,但在复杂模型和特定应用场景下,手动调整仍然是优化支撑结构的重要手段。手动调整可以帮助用户根据实际需求进行细化的设计,进一步提高打印效果。
1. 手动调整支撑类型
对于一些复杂或精细的3D模型,软件自动生成的支撑结构可能并不完全理想。这时,用户可以手动调整支撑的类型和位置。例如,可以根据模型的特殊结构,选择使用树枝状支撑,减少支撑接触点与模型的接触面积,方便后期拆除。手动调整还可以帮助避免支撑结构与模型表面的接触,从而减少后期清理的难度。
2. 选择合理的支撑位置
手动调整还可以帮助用户选择支撑的具体位置,避免不必要的支撑生成。例如,对于一些小而精致的部件,用户可以通过选择打印角度,使得模型的悬空部分减少,进而减少对支撑结构的需求。通过合理选择支撑位置,既能提高打印效率,又能降低后期处理的复杂性。
3. 控制支撑的接触面
支撑结构的接触面与模型表面直接影响到后处理的难度。通过手动调整,用户可以控制支撑的接触面大小,减少与模型表面的接触面积,降低拆除难度和后期的表面处理工作量。此外,合理的接触面设计还可以有效降低支撑结构的强度,使得拆除过程更加简便。
五、总结
3D打印模型的支撑结构设计和优化是一个复杂且具有挑战性的过程,涉及到打印质量、材料浪费、后处理和打印时间等多方面的考量。通过合理利用软件算法和手动调整两者的优势,用户可以在满足支撑需求的同时,最大限度地减少不必要的支撑结构,提高打印效率,降低后期处理难度。随着3D打印技术的不断进步,支撑优化的方式将变得更加智能化和高效化,未来的3D打印将会更加精细和多样化。